3.1. Introducción.
Los firmes con pavimento bituminoso se clasifican en tres categorías principales:
1. Firmes flexibles: Estos firmes se caracterizan por tener una estructura que se deforma bajo cargas de tráfico, distribuyendo las tensiones a través de las capas inferiores. Están compuestos por una capa de rodadura de asfalto sobre una base granular y, en algunos casos, una subbase. La capa de rodadura proporciona resistencia al desgaste y a la penetración del agua.
2. Firmes semi-flexibles: Estos firmes presentan características intermedias entre los firmes flexibles y los firmes semirrígidos. Tienen una mayor rigidez que los firmes flexibles, pero aún permiten cierta deformación bajo carga. Generalmente consisten en una capa de rodadura de asfalto sobre una base granular más espesa o reforzada con materiales como cemento.
3. Firmes semirrígidos: Estos firmes tienen una estructura más rígida y resistente a la deformación que los firmes flexibles. Son adecuados para áreas con tráfico pesado o donde se requiere una mayor durabilidad. Están compuestos por una capa de rodadura de asfalto sobre una base de hormigón, con o sin capas intermedias de refuerzo.
La elección entre estos tipos de firmes depende de varios factores, como el volumen y tipo de tráfico, las condiciones climáticas, el presupuesto disponible y la disponibilidad de materiales locales.
En el caso de los firmes con pavimento de hormigón, se clasifican como firmes rígidos. Estos firmes se caracterizan por tener una estructura sólida y resistente, con una capa de hormigón como superficie de rodadura. Son adecuados para áreas con tráfico intenso y donde se requiere una alta resistencia y durabilidad.
Otros tipos de firmes incluyen:
1. Firmes adoquinados: Estos firmes están compuestos por adoquines de piedra, concreto u otros materiales colocados sobre una base de arena o grava. Son comunes en áreas peatonales o en calles históricas donde se busca un aspecto tradicional.
2. Firmes mixtos: Estos firmes combinan diferentes materiales, como asfalto y hormigón, en distintas capas para aprovechar las ventajas de cada uno. Por ejemplo, pueden tener una base de hormigón con una capa de asfalto como superficie de rodadura.
3. Firmes sin pavimentar: Estos firmes no tienen una capa de rodadura pavimentada y consisten en el suelo natural o materiales granulares compactados. Son comunes en áreas rurales o caminos secundarios donde no se requiere una superficie pavimentada.
En cuanto a la clasificación de los firmes flexibles y semiflexibles, se consideran firmes flexibles aquellos constituidos por capas granulares no tratadas y materiales bituminosos con un espesor inferior a 15 cm. Si el espesor de los materiales bituminosos es igual o superior a 15 cm sobre capas granulares no tratadas, se consideran semiflexibles. Esta distinción se basa en la capacidad de deformación de la estructura bajo la carga del tráfico.
Exactamente, los firmes flexibles, también conocidos como pavimentos asfálticos, se componen de una capa de asfalto sobre una base de material granular compactado. Estos firmes son flexibles y pueden soportar cargas vehiculares distribuyendo las fuerzas a lo largo de la estructura. Son comunes en carreteras, calles urbanas y áreas con tráfico ligero a pesado.
Por otro lado, los firmes rígidos están formados por una losa de hormigón como superficie de rodadura. Estos firmes son más robustos y resistentes, adecuados para áreas con tráfico pesado y donde se requiere una alta durabilidad. Son comunes en autopistas, aeropuertos y áreas industriales.
En algunos casos, se utilizan firmes mixtos, que combinan características de los firmes flexibles y rígidos. Por ejemplo, pueden tener una base de hormigón con una capa de asfalto como superficie de rodadura. Esto permite aprovechar las ventajas de ambos tipos de firmes.
Entonces, utilizando esta nomenclatura, por ejemplo, una sección de firme con el número 4214 indicaría lo siguiente:
- La primera cifra (4) indica que está diseñada para soportar tráfico pesado de categoría T42.
- La cifra penúltima (2) indica que la explanada corresponde a la categoría E2.
- La última cifra (4) señala que el tipo de firme es un pavimento de hormigón.
Esta convención permite una rápida identificación de las características principales de una sección de firme, lo que facilita su diseño y gestión.
Estas son las capas que conforman un firme flexible típico en las carreteras españolas:
Capa anticontaminante o capa filtro: Esta capa se coloca sobre la explanada en casos específicos, especialmente cuando el suelo es arcilloso y puede hincharse con la humedad, lo que podría dañar el pavimento. Su función es evitar que la humedad llegue a las capas superiores y cause daños.
Explanada mejorada: Se sitúa sobre la explanada o la capa filtro (si se ha colocado). Está compuesta por un suelo granular seleccionado para proporcionar una superficie adecuada que pueda soportar las capas superiores del firme. Su espesor se determina según los requerimientos de diseño y las condiciones del terreno.
Subbase: Esta capa se encuentra debajo de la base y sobre la explanada mejorada. Se utiliza para construir la zahorra, que puede estar compuesta por gravas, arenas naturales o trituradas, escorias u otros materiales seleccionados. La subbase proporciona un cimiento uniforme sobre el cual se asienta la base.
Base: La base se sitúa directamente debajo del pavimento y es crucial para distribuir las cargas del tráfico de manera uniforme hacia las capas inferiores del firme. Debe ser lo suficientemente resistente para soportar estas cargas sin deformarse significativamente.
Pavimento: Es la capa superior del firme y es la que está en contacto directo con el tráfico. Está compuesto por varias subcapas, siendo la superior la capa de rodadura, que es la que realmente soporta las cargas de tráfico y proporciona la superficie de rodaje. El pavimento puede estar formado por mezclas bituminosas, concreto asfáltico u otros materiales, dependiendo de las especificaciones del proyecto y las condiciones del tráfico.
Los firmes rígidos, como su nombre lo indica, están compuestos principalmente por una capa de hormigón hidráulico que forma el pavimento. Aquí hay un desglose más detallado de las capas que componen los firmes rígidos:
Subbase o base: Esta capa se encuentra debajo del pavimento de hormigón y proporciona un soporte uniforme para la base de hormigón. Además de ofrecer una superficie nivelada, la subbase/base también debe tener propiedades drenantes y anticontaminantes para proteger la integridad del pavimento.
Base de hormigón hidráulico: Es la capa superior del firme rígido y está formada por hormigón hidráulico, que es una mezcla de cemento, áridos y agua. Esta capa forma la superficie de rodadura y soporta directamente las cargas del tráfico. El espesor de la base de hormigón puede variar dependiendo de los requisitos de diseño y las condiciones del tráfico, pero generalmente puede llegar a tener entre 20 y 30 cm de espesor.
Juntas transversales y longitudinales: Se realizan juntas transversales cada cierta distancia, típicamente cada 5 o 6 metros, para permitir la expansión y contracción del hormigón debido a los cambios de temperatura y evitar la formación de grietas. Además, se instala una junta longitudinal en el eje de la carretera para controlar las fisuras que pueden ocurrir debido a la contracción del hormigón.
Estos elementos son fundamentales para garantizar la durabilidad y el buen desempeño de los firmes rígidos en las carreteras. La calidad de la base de hormigón y la correcta instalación de las juntas son especialmente importantes para evitar problemas como el agrietamiento prematuro y mantener la integridad estructural del pavimento a lo largo del tiempo.
Las subbases y bases granulares son componentes fundamentales en los firmes flexibles. Aquí hay una descripción más detallada de estas capas:
Subbase: La subbase es la capa inferior de material granular que se encuentra debajo de la base en un firme flexible. Está compuesta principalmente por partículas minerales como grava, arena y piedra triturada, sin ningún aglutinante o ligante. La función principal de la subbase es proporcionar un soporte uniforme y estable para la base y el pavimento superior. Distribuye las cargas del tráfico sobre un área más amplia, ayudando a prevenir la deformación excesiva del suelo subyacente.
Base: La base es la capa superior de material granular en un firme flexible. También está compuesta por partículas minerales sin ningún ligante. Su objetivo principal es distribuir uniformemente las cargas del tráfico transmitidas por el pavimento superior (capa de rodadura) hacia la subrasante o terreno subyacente. Además, proporciona una superficie sólida y resistente para el pavimento superior. La base es crucial para la estabilidad y durabilidad general del firme flexible.
En resumen, tanto la subbase como la base granular son esenciales para la adecuada distribución de cargas y la estabilidad de los firmes flexibles, permitiendo que la estructura del pavimento resista las presiones del tráfico sin deformarse excesivamente.
Las especificaciones técnicas generales españolas para la subbase suelen incluir requisitos específicos sobre los materiales a utilizar y sus características granulométricas. Aquí tienes un resumen de algunas de estas especificaciones:
- Materiales permitidos: Se permiten tanto áridos naturales como áridos de machaqueo. Estos materiales deben cumplir con ciertos estándares de calidad y características específicas para garantizar su idoneidad para su uso en la subbase.
- Requisitos granulométricos: Se establecen criterios precisos sobre la distribución del tamaño de las partículas en los materiales de la subbase. Algunas de estas especificaciones incluyen:
- La fracción en peso que pasa por el tamiz número 200 debe ser menor que los 2/3 de la fracción que pase por el tamiz número 40. Esto significa que la proporción de partículas finas debe ser controlada para evitar un exceso de material fino que pueda afectar negativamente las propiedades de la subbase.
- Se establece una curva granulométrica específica que los materiales deben cumplir. Esta curva determina la distribución de tamaños de partículas en los materiales de la subbase y es crucial para garantizar su adecuación para el uso previsto en la construcción del firme.
Las especificaciones detalladas sobre los materiales y las características granulométricas se proporcionan para asegurar que la subbase cumpla con los estándares de calidad y rendimiento necesarios para brindar un soporte adecuado a la base y al pavimento superior en la estructura del firme.
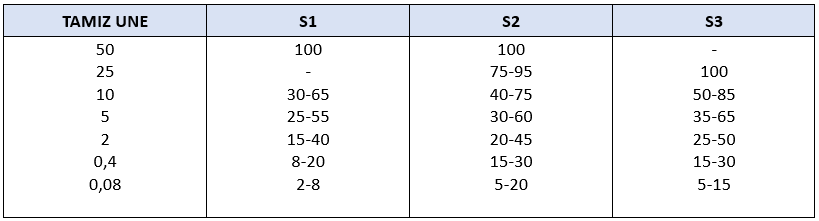
Las especificaciones adicionales para la puesta en obra de la subbase incluyen:
- Densidad de compactación: Se requiere que la subbase alcance una densidad de compactación del 95% del Proctor Modificado. Esto asegura que el material esté lo suficientemente compactado para proporcionar un soporte adecuado y resistencia a la deformación bajo las cargas del tráfico.
- Evitar segregación en los bordes: Durante la colocación y compactación de la subbase, es importante evitar la segregación, que es la separación de los diferentes tamaños de partículas. Esto garantiza una distribución uniforme de los materiales y una mayor cohesión en toda la capa de subbase.
- Uniformidad de la superficie: Se establece un criterio de uniformidad para la superficie de la subbase. Se especifica que la variación en la superficie no debe exceder los 10 mm al medir con una regla de 3 metros. Esto asegura una superficie nivelada y uniforme, que es fundamental para la colocación adecuada de las capas subsiguientes del firme y para garantizar un rendimiento óptimo del pavimento.
Bases
Las bases granulares se dividen en dos tipos principales: las de tipo MACADAM, que presentan una granulometría discontinua, y las de tipo ZAHORRA ARTIFICIAL, que tienen una granulometría continua.
El diseño de las bases MACADAM se remonta al ingeniero escocés John Loudon McAdam, quien en 1820 propuso un pavimento compuesto por áridos gruesos de tamaño uniforme, los cuales se compactaban y se rellenaban los huecos con un material fino conocido como recebo.
A lo largo del tiempo, los pavimentos MACADAM, e incluso variantes asfálticas como el MACADAM Asfáltico por penetración, fueron ampliamente utilizados. Sin embargo, en la actualidad, estos pavimentos están en declive debido a su capacidad de soporte limitada, los costos asociados con su colocación y la escasez de materiales pétreos de calidad, lo que los hace menos rentables.
Al igual que en el caso de las subbases, existen requisitos específicos para los áridos utilizados en las bases MACADAM y en el recebo.
Las bases granulares de zahorra artificial se distinguen de las de tipo MACADAM por su granulometría continua, lo que significa que incluyen áridos de diversos tamaños en proporciones similares, en contraste con el MACADAM, que consiste en árido grueso y árido fino o recebo. Una especificación importante para la zahorra artificial es que al menos el 50% de los áridos deben tener dos o más caras de fractura, lo que indica que son materiales de machaqueo.
Aunque las bases granulares a veces no proporcionan la resistencia deseada, se puede recurrir a los suelos estabilizados para mejorar sus propiedades. Estos suelos estabilizados, como la gravacemento y el suelo-cemento, están ganando popularidad para las capas de base y subbase.
La gravacemento y el suelo-cemento son mezclas de suelo con una proporción controlada de cemento y agua. A diferencia del hormigón, la cantidad de cemento es relativamente baja, de modo que los granos del suelo no quedan completamente envueltos por el cemento, sino que solo se unen parcialmente entre sí. Los porcentajes de cemento típicos oscilan entre el 5% y el 10% en peso del suelo.
3.2. Áridos
Los áridos de construcción son materiales granulares inorgánicos compuestos por fragmentos de grava, gravilla y arena de diferentes tamaños. Son químicamente estables y mecánicamente resistentes, lo que los hace fundamentales en la construcción de diversas estructuras, desde viviendas hasta carreteras e infraestructuras.
Existen dos tipos principales de áridos según su origen y proceso de obtención:
- Áridos naturales: Estos áridos se extraen de yacimientos geológicos utilizando métodos mecánicos. Pueden provenir de depósitos no consolidados, como graveras, donde se utilizan maquinaria convencional, o de macizos rocosos, donde se requieren técnicas específicas como voladuras con explosivos en canteras. Los áridos naturales se dividen en dos grandes grupos:
- Áridos granulares: Proceden principalmente de graveras que explotan depósitos granulares. Estos áridos se someten a lavado y clasificación antes de su uso. Tienen forma redondeada, superficies lisas y no presentan aristas, por lo que se les llama áridos rodados. Son predominantemente de naturaleza silícea.
- Áridos de machaqueo: Se producen en canteras después de extraer los materiales de los macizos rocosos y someterlos a trituración, molienda y clasificación. Estos áridos tienen superficies rugosas y aristas vivas. Son principalmente de naturaleza caliza, aunque también pueden ser silíceos.
Además de los áridos naturales, también existen otros tipos de áridos utilizados en la construcción:
- Áridos reciclados: Provenientes del tratamiento de residuos de construcción y demolición. Estos áridos se obtienen mediante la trituración y clasificación de los materiales reciclados, como el hormigón, el asfalto, la cerámica, entre otros.
- Áridos artificiales: Resultan de procesos industriales que implican modificaciones físico-químicas u otros métodos. Por ejemplo, las escorias de alto horno son un tipo de árido artificial obtenido como residuo del proceso siderúrgico.
El árido siderúrgico es un ejemplo de árido artificial que se obtiene tras un tratamiento adecuado de las escorias valorizables generadas en la industria siderúrgica. Estas escorias son residuos derivados de varias etapas del proceso siderúrgico, como la fabricación de arrabio en hornos altos, la producción de acero mediante afino de arrabio en hornos convertidores y la producción de acero a partir de chatarra en hornos de arco eléctrico. Después de triturarse, clasificarse y desferrizarse, estas escorias se convierten en un material apto para su uso como árido en la construcción.
Los áridos gruesos son aquellos que quedan retenidos en el tamiz de 4 mm según la norma UNE-EN 933-2.
Los áridos gruesos son fundamentales en la construcción de carreteras, ya que forman el esqueleto mineral que proporciona resistencia estructural al pavimento. La interacción entre los áridos crea una estructura cohesiva capaz de soportar las cargas del tráfico.
Para que un árido grueso sea adecuado para su uso en carreteras, debe cumplir con varios requisitos relacionados con su resistencia mecánica, forma, angulosidad, limpieza, adhesividad y resistencia al pulido. A continuación, se detallan brevemente cada uno de estos requisitos:
1. Resistencia mecánica: El árido debe ser capaz de resistir las fuerzas y tensiones generadas por el tráfico vehicular y otras cargas. Esto se evalúa mediante ensayos de laboratorio, como el ensayo de desgaste Los Ángeles, que mide la resistencia a la fragmentación por abrasión.
2. Forma y angulosidad: Se busca minimizar la presencia de áridos planos o alargados, ya que estas partículas tienden a romperse con facilidad. Es importante que cada árido tenga múltiples planos de fractura para garantizar su estabilidad. Se realizan ensayos para medir la proporción de áridos con formas no deseadas, como lajas o agujas.
3. Limpieza: La presencia de polvo, suciedad, arcillas u otras impurezas puede afectar negativamente la calidad del árido y su capacidad para adherirse al ligante. Se realizan ensayos para determinar el grado de limpieza del árido y tomar decisiones sobre su idoneidad para su uso en carreteras.
4. Adhesividad: Es crucial que el árido tenga la capacidad de adherirse al ligante, ya sea asfáltico o de cemento, para garantizar la resistencia y durabilidad del pavimento. Se realizan ensayos para evaluar esta propiedad y determinar la calidad del árido en términos de su capacidad de adherencia al ligante.
5. Resistencia al pulido: El árido debe mantener su rugosidad superficial a lo largo del tiempo, especialmente bajo las condiciones de tráfico y clima. La resistencia al pulido se evalúa mediante ensayos que simulan el desgaste producido por el tráfico vehicular, ayudando a determinar la pérdida de textura superficial del árido.
Cumplir con estos requisitos es esencial para asegurar la calidad y el rendimiento del árido grueso en la construcción de carreteras, contribuyendo así a la durabilidad y seguridad de la infraestructura vial.
Áridos finos
Se define como árido fino a la parte del árido total cernida por el tamiz 4 mm de la norma UNE-EN 933-2.
Los áridos finos desempeñan un papel crucial en la construcción de carreteras al llenar los espacios entre los áridos gruesos en una capa de firme. Para ser adecuados en la construcción vial, los áridos finos deben cumplir con una serie de requisitos específicos. La clave para evaluar la calidad de un árido fino es comprender que cuanto mayor sea el contenido de arcilla, peor será su calidad. Esto se debe a que las arcillas tienden a ablandarse y perder resistencia cuando se mojan. La determinación del contenido de arcilla se realiza indirectamente mediante ensayos como los límites de Atterberg o el equivalente de arena.
Los áridos finos de calidad deben ser no plásticos y tener un alto equivalente de arena. La adhesividad del árido fino al ligante es también un factor importante, especialmente en la fabricación de mezclas bituminosas. Esta propiedad puede evaluarse mediante ensayos normalizados. Es importante destacar que los áridos finos utilizados en mezclas bituminosas deben provenir de la trituración de piedra de cantera o grava natural.
Cumplir con estos requisitos garantiza que los áridos finos contribuyan de manera efectiva a la calidad y durabilidad del pavimento, asegurando una buena adherencia al ligante y una correcta compactación en la construcción de carreteras.
Un árido combinado es aquel que consiste en una mezcla de áridos gruesos y finos, sin una separación previa en fracciones de áridos finos y gruesos. Esta combinación puede lograrse de varias formas, ya sea mezclando directamente áridos de diferentes tamaños o combinando fracciones independientes de áridos finos y gruesos. En esencia, un árido combinado aprovecha las características de los áridos gruesos y finos para cumplir con los requisitos específicos de una aplicación particular, como la construcción de carreteras, pavimentos u otras obras civiles.
Zahorras
Las zahorras son materiales granulares utilizados como capa de firme en la construcción de carreteras u otras obras. Se definen por su granulometría continua, lo que significa que contienen partículas de todos los tamaños. Esto les confiere varias ventajas, como una compacidad elevada, un aumento en los puntos de contacto entre las partículas y una reducción del riesgo de atrición.
Existen dos tipos principales de zahorras:
Zahorra artificial: Se compone de partículas total o parcialmente trituradas de piedra de cantera o grava natural. La proporción de trituración puede variar según las especificaciones de cada proyecto.
Zahorra natural: Está compuesta principalmente por partículas no trituradas, provenientes de graveras, depósitos naturales o una combinación de ambos. Sin embargo, este tipo de zahorra no se contempla en el Pliego de Prescripciones Técnicas Generales.
Ambos tipos de zahorras se utilizan como base o subbase en la construcción de carreteras debido a su capacidad para soportar cargas y proporcionar una superficie adecuada para la circulación vehicular.
La ejecución de las capas de firme con zahorra implica varias operaciones clave:
Estudio del material y obtención de la fórmula de trabajo: Se realiza un análisis del material de zahorra disponible para determinar su idoneidad y características. Además, se establece la fórmula de trabajo que especifica la composición y las proporciones adecuadas de los materiales.
Preparación de la superficie existente: Antes de colocar la zahorra, se prepara la superficie existente eliminando cualquier material suelto, escombros u obstrucciones que puedan afectar a la calidad de la capa de firme.
Preparación del material y transporte: Si es necesario, se realiza un tratamiento previo al material de zahorra para adecuarlo a las especificaciones requeridas. Luego, se transporta el material al lugar de trabajo utilizando equipos apropiados.
Extensión, humectación y compactación: Una vez en el lugar, se extiende la zahorra sobre la superficie preparada en capas uniformes. En caso necesario, se humecta el material para facilitar la compactación. Posteriormente, se compacta la zahorra utilizando equipos adecuados para lograr la densidad y resistencia requeridas.
Es importante destacar que los materiales utilizados para las capas de zahorra deben cumplir con estándares de calidad que garanticen su estabilidad y resistencia a condiciones adversas, como la acción del agua, para evitar daños a la estructura del firme o contaminación ambiental.
3.3. Riegos bituminosos.
Los riegos bituminosos son aplicaciones de emulsiones bituminosas sobre diferentes capas de una carretera con el fin de mejorar la adherencia entre las capas, impermeabilizar la superficie y mejorar su durabilidad. Aquí tienes algunas definiciones clave:
Riego de imprimación: Consiste en aplicar una emulsión bituminosa sobre una capa granular antes de colocar una capa bituminosa encima. Este proceso prepara la superficie para mejorar la adherencia de la capa bituminosa y proporcionar una superficie uniforme y sellada.
Árido de cobertura: Se refiere al material granular, como arena natural o arena de machaqueo, que se esparce sobre la emulsión bituminosa aplicada durante el riego de imprimación. Este árido de cobertura ayuda a mejorar la adherencia y proporciona una superficie adecuada para la colocación de la capa bituminosa.
Riego de adherencia: Se utiliza para aplicar una emulsión bituminosa sobre una capa que ya ha sido tratada con ligantes hidrocarbonados o conglomerantes hidráulicos. Este riego ayuda a mejorar la unión entre las capas existentes y la nueva capa bituminosa que se aplicará encima.
Riego de curado: Se aplica una película continua y uniforme de emulsión bituminosa sobre una capa tratada con un conglomerante hidráulico. El objetivo es impermeabilizar la superficie y evitar la evaporación del agua necesaria para que el conglomerante hidráulico fragüe correctamente, mejorando así la resistencia y durabilidad de la capa.
3.4. El hormigón
El hormigón es un material esencial en la construcción de carreteras debido a su versatilidad y resistencia. Aquí tienes algunos elementos comunes de las carreteras que se fabrican con hormigón:
– Estructuras de hormigón armado o pretensado: Incluyen elementos como puentes, muros de contención, losas para pasos subterráneos y túneles. El hormigón armado se refuerza con barras de acero para aumentar su resistencia, mientras que el hormigón pretensado tiene cables de acero pretesados que proporcionan una mayor resistencia y durabilidad.
– Pavimentos de hormigón: Se utilizan para carreteras de alto tráfico y zonas donde se requiere una mayor resistencia y durabilidad. Los pavimentos de hormigón ofrecen una superficie uniforme y resistente que puede soportar cargas pesadas y condiciones climáticas adversas.
– Revestimiento de cunetas: El hormigón se utiliza para revestir cunetas y canales de drenaje a lo largo de la carretera, proporcionando una superficie resistente a la erosión y facilitando el drenaje adecuado del agua de lluvia.
– Rellenos: En algunas situaciones, se utilizan rellenos de hormigón para estabilizar el terreno y proporcionar una base sólida para la construcción de la carretera.
– Revestimientos mediante hormigón proyectado: También conocido como gunita, se utiliza para aplicar una capa de hormigón sobre superficies irregulares o en áreas de difícil acceso, como taludes o muros de contención.
– Prefabricados de hormigón: Se fabrican elementos prefabricados de hormigón para su uso en diferentes partes de la carretera, como barreras de seguridad, señalización vial, postes de iluminación y elementos decorativos.
Estos son solo algunos ejemplos de cómo se utiliza el hormigón en la construcción y mantenimiento de carreteras, demostrando su importancia en la infraestructura vial.
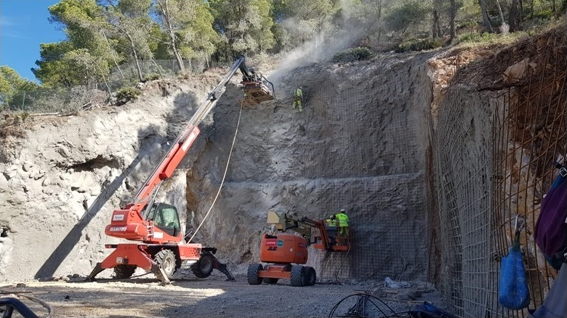
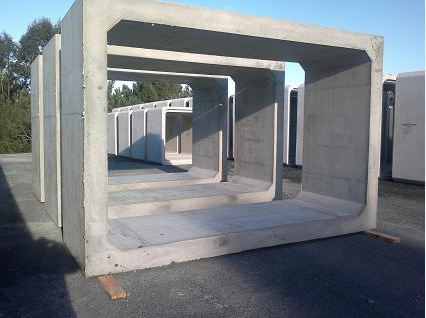
El hormigón estructural es aquel que incluye refuerzos, como barras o alambres de acero, para mejorar su resistencia a la tracción. Este tipo de hormigón se utiliza en elementos donde se requiere una mayor resistencia, como en vigas, columnas y losas de edificios, puentes y otras estructuras.
Cuando las armaduras en el hormigón son pasivas, es decir, solo comienzan a experimentar tensiones cuando el hormigón está cargado, se denomina hormigón armado. En cambio, cuando las armaduras están sometidas a tensiones antes de que el elemento de hormigón sea cargado, se llama hormigón pretensado.
El hormigón armado se utiliza comúnmente en la construcción de estructuras de todo tipo, mientras que el hormigón pretensado se emplea en aplicaciones donde se requiere una mayor resistencia y durabilidad, como en puentes de gran luz y losas de pavimento de carreteras.
Los hormigones se tipifican de acuerdo con el siguiente formato:
T-R/C/TM/A
- T: Este indicativo se refiere al tipo de hormigón. Se utiliza “HM” para el hormigón en masa, “HA” para el hormigón armado y “HP” para el hormigón pretensado.
- R: Representa la resistencia característica especificada del hormigón, medida en Newtons por milímetro cuadrado (N/mm²).
- e: Es la letra inicial que denota el tipo de consistencia del hormigón. Por ejemplo, “B” para un hormigón blando o “S” para un hormigón semifluido.
- TM: Se refiere al tamaño máximo del árido utilizado en el hormigón, medido en milímetros.
- A: Es la designación del ambiente en el que se utilizará el hormigón. Por ejemplo, puede ser “X” para un ambiente agresivo o “N” para un ambiente normal.
Supongamos que tenemos un hormigón armado con una resistencia característica especificada de 30 N/mm², una consistencia del tipo “Blanda”, un tamaño máximo del árido de 20 mm y que estará expuesto a un ambiente marino. La tipificación sería la siguiente:
HA-30/B/20/M
Esto indica que se trata de hormigón armado (HA) con una resistencia característica de 30 N/mm², una consistencia blanda (B), un tamaño máximo del árido de 20 mm y estará expuesto a un ambiente marino (M).
Esta forma de tipificación facilita la identificación y especificación del tipo de hormigón necesario para cada aplicación y ambiente de trabajo.
En cuanto a la resistencia característica especificada, se recomienda utilizar la si guiente serie:
20, 25, 30, 35, 40, 45, 50,
La serie recomendada de resistencia característica especificada para el hormigón. Es útil saber que se recomienda seguir la serie de resistencia de 20, 25, 30, 35, 40, 45 y 50 N/mm². Esto proporciona una gama de opciones para adaptarse a diferentes requisitos de resistencia en diversas aplicaciones de construcción.
Es importante tener en cuenta que la resistencia de 20 N/mm² está limitada a la utilización en hormigones en masa, lo que sugiere que este tipo de hormigón puede ser adecuado para aplicaciones específicas donde se requiere una resistencia más baja pero aún así se busca cierto nivel de durabilidad y estabilidad.
La consistencia de un concreto se refiere a cuán fluido está cuando está recién mezclado y antes de que comience a fraguar. Esta medida clasifica el concreto en diferentes tipos de consistencia: seca, plástica, blanda, fluida y líquida.
La consistencia seca se emplea principalmente en la fabricación de elementos prefabricados, mientras que la plástica y la blanda son las más comunes en el concreto que se transporta a las obras en camiones mezcladores, con la blanda siendo especialmente prevalente.
Las armaduras dentro del concreto tienden a oxidarse más rápido si están demasiado cerca de la superficie, lo que se conoce como recubrimiento. En regiones costeras, este recubrimiento debe ser más generoso que en áreas interiores debido al entorno corrosivo generado por la presencia de cloruros en el aire marino. Este ambiente también influye en la formulación de los ingredientes del concreto. Los distintos entornos, conocidos como clases de exposición, se clasifican de la siguiente manera: no agresiva (tipo I), normal (tipo II), marina (III) y con cloruros de origen no marino (tipo IV). Aunque hay más categorías de ambientes, no es necesario detallarlos todos en este contexto.
El método más simple para colocar concreto en el sitio de trabajo implica verterlo desde el equipo de transporte (como una cuba o cubilote) directamente al encofrado, molde o área de destino. Es esencial evitar que el concreto caiga libremente desde alturas superiores a dos metros para evitar la segregación de los componentes y posibles daños a los encofrados. Además, se debe evitar colocar capas de concreto cuyo espesor supere el límite que permita su compactación completa, generalmente entre 30 y 60 cm, dependiendo de los métodos de compactación y la forma del encofrado.
En la producción de concreto, si no se utilizan aditivos retardadores, el tiempo entre la adición de agua a la mezcla de cemento y agregados y la colocación del concreto en el sitio de trabajo no debe exceder una hora y media.
Se prohíbe expresamente agregar agua u otras sustancias al concreto que puedan alterar su composición original. La adición de agua puede resultar en una disminución de la resistencia del concreto y provocar la formación de fisuras.
Encofrado
El encofrado, ya sea metálico o de madera, es crucial en la construcción para dar forma al hormigón fresco.
- Las chapas metálicas son fáciles de montar y tienen una larga vida útil, pero pueden resultar difíciles de adaptar a formas irregulares. Al unirse, pueden dejar marcas en la superficie del muro o pilar una vez que el concreto ha endurecido. Sin embargo, el uso de aluminio puede ser problemático, ya que puede reaccionar con los iones OH- presentes en el agua del concreto fresco, generando burbujas de gas hidrógeno (H2). Además, el aluminio puede corroerse y dañar el hormigón, especialmente en presencia de acero y altos niveles de cloruros o álcalis en la solución de poros.
- Por otro lado, los tableros de encofrado son más ligeros y pueden adaptarse fácilmente a formas irregulares. El tipo de madera utilizado puede influir en el acabado final del concreto. Sin embargo, estos tableros tienden a degradarse más rápidamente y requieren un cuidado especial en términos de mantenimiento y montaje.
Para la construcción de pilares, es común utilizar tubos de encofrado de cartón, que vienen en una variedad de medidas, formas (como pilares circulares, cuadrados, esquineros, entre otros) y acabados. Estos tubos son desechables y se caracterizan por ser fáciles de manejar, instalar y retirar.
En todos los casos, las características principales de los materiales para encofrar son:
- Rigidez y resistencia, para soportar el peso del hormigón y mantener la forma deseada.
- Estanqueidad, asegurando que las juntas sean herméticas para prevenir fugas de hormigón y defectos en la superficie de la estructura.
- Resistencia a la acción del agua, aditivos y otros componentes del hormigón.
- No adherencia fuerte al hormigón una vez seco, permitiendo una extracción fácil.
Además, los puntales son elementos auxiliares indispensables en el encofrado. Consisten en barras de hierro que actúan temporalmente como apoyo o soporte de la estructura de chapas o tableros de encofrado hasta que el hormigón fragüe y se sostenga por sí mismo.
Pavimentos de hormigón
El pavimento de hormigón se define como un conjunto de losas de hormigón en masa separadas por juntas transversales, o como una losa continua de hormigón armado, ocasionalmente con juntas longitudinales. Este tipo de pavimento requiere que el hormigón se coloque con una consistencia que necesite el uso de vibradores internos para compactarlo, así como maquinaria específica para su extensión y acabado superficial.
Se pueden distinguir varios tipos de pavimentos de hormigón:
1. Pavimento rígido: Compuesto por losas de hormigón en masa separadas por juntas transversales y, en algunos casos, juntas longitudinales.
2. Pavimento de hormigón armado: Formado por una losa continua de hormigón reforzado con acero, con o sin juntas longitudinales.
3. Pavimento de hormigón reforzado con mallas o fibras: Similar al pavimento de hormigón armado, pero en lugar de barras de acero, se utiliza una malla metálica o fibras para reforzar el hormigón y controlar las fisuras.
4. Pavimento de hormigón impreso: Se caracteriza por tener una superficie decorativa que imita diferentes materiales, como piedra, ladrillo o baldosas, mediante el uso de moldes y colorantes aplicados en la superficie del hormigón fresco.
5. Pavimento de hormigón pulido: Consiste en un pavimento de hormigón cuya superficie se pule mecánicamente para lograr un acabado liso y brillante, adecuado para áreas de alto tráfico peatonal o vehicular.
Entre ellos:
- Pavimento de hormigón con juntas: Este tipo de pavimento consiste en losas de hormigón en masa con juntas transversales colocadas a intervalos regulares, generalmente entre tres y cinco metros. Estas juntas permiten la transferencia de cargas entre las losas, y pueden ser gestionadas mediante pasadores de acero o dejando que los áridos se encajen entre sí.
- Pavimento de hormigón armado continuo: En este caso, el pavimento de hormigón está reforzado con armadura longitudinal continua y no tiene juntas transversales de contracción o, en algunos casos, dilatación.
Ambos tipos de pavimento pueden ser construidos en una sola capa o en dos capas sucesivas con un desfase mínimo para asegurar una buena adherencia entre ellas. En el segundo caso, la capa superior de hormigón se suele diseñar para recibir un tratamiento que elimine el mortero superficial, dejando expuesto el árido grueso para resistir la acción directa del tráfico.
La ejecución del pavimento de hormigón implica una serie de operaciones que incluyen:
1. Estudio y obtención de la fórmula de trabajo, que determina la composición adecuada del hormigón para las condiciones específicas del proyecto.
2. Preparación de la superficie de asiento, asegurando que esté limpia, nivelada y libre de materiales sueltos.
3. Fabricación del hormigón, mezclando los materiales según la fórmula establecida y asegurando su homogeneidad.
4. Transporte del hormigón desde la planta de fabricación hasta el lugar de trabajo.
5. Colocación de elementos de guía y preparación de los caminos de rodadura para la pavimentadora y otros equipos de acabado superficial.
6. Colocación de los elementos de las juntas, que pueden ser transversales o longitudinales, según el tipo de pavimento.
7. Colocación de armaduras en el caso de pavimentos continuos de hormigón armado.
8. Puesta en obra del hormigón, extendiéndolo y compactándolo adecuadamente con equipos especializados.
9. Ejecución de juntas longitudinales y, si es necesario, juntas transversales mientras el hormigón está fresco.
10. Terminación de bordes y aplicación de la textura superficial deseada.
11. Protección y curado del hormigón fresco para asegurar su adecuado fraguado y resistencia.
12. Ejecución de juntas transversales serradas y, en algunos casos, juntas longitudinales después del fraguado del hormigón.
13. Sellado de las juntas para prevenir filtraciones y daños en el pavimento.
A) Hormigonado en tiempo frío
El hormigonado en tiempo frío se refiere a la colocación de concreto durante un período en el que prevalecen bajas temperaturas. Se considera que hay tiempo frío cuando se cumplen las siguientes condiciones durante más de tres días:
- La temperatura media diaria del aire es inferior a 5 ºC.
- La temperatura del aire no supera los 10 ºC durante más de la mitad del día.
Las bajas temperaturas retardan la hidratación de la pasta de cemento, lo que puede afectar el proceso de fraguado y endurecimiento del concreto. Además, existe el riesgo de daño permanente si el concreto fresco se congela, ya que el agua contenida en los poros puede expandirse al congelarse y romper el material.
Por lo tanto, es crucial tomar medidas para asegurar que el concreto endurezca a una velocidad adecuada y para prevenir daños por congelación. Esto puede implicar el uso de aditivos aceleradores de fraguado, mantas térmicas para mantener la temperatura del concreto, o programar el vertido del concreto en momentos del día con temperaturas más favorables.
Para contrarrestar los efectos del tiempo frío en el hormigonado, se pueden implementar varias medidas en la dosificación del concreto. Por ejemplo, se puede optar por utilizar relaciones agua/cemento lo más bajas posible y aumentar el contenido de cemento, o incluso emplear cementos de mayor categoría resistente. Estas acciones tienen como objetivo acelerar la velocidad de endurecimiento del concreto, elevar su temperatura y reducir el riesgo de congelación.
Cuando existe riesgo de hielo o de heladas prolongadas, es crucial proteger el concreto fresco. Esto se puede lograr mediante dispositivos de cobertura o aislamiento, o incluso mediante cerramientos que permitan el calentamiento del aire que rodea al elemento estructural recién hormigonado. En este último caso, es importante tomar medidas para mantener la humedad adecuada en el concreto y asegurar que el proceso de fraguado se desarrolle de manera óptima.
Para garantizar la calidad y resistencia del hormigón en condiciones de temperatura fría, se establecen ciertas normativas y precauciones:
1. La temperatura de la masa de hormigón al verterla en el molde o encofrado no debe ser inferior a 5 ºC.
2. Queda prohibido verter el hormigón sobre elementos cuya temperatura sea inferior a cero grados centígrados.
3. Si se prevé que la temperatura ambiente descenderá por debajo de cero grados centígrados en las cuarenta y ocho horas siguientes, se suspende el hormigonado.
4. En situaciones de heladas inevitables, se deben tomar medidas para prevenir daños locales en los elementos de concreto y evitar reducciones permanentes en sus propiedades resistentes. Si se produce algún daño, se deben realizar pruebas para evaluar la resistencia del concreto y tomar medidas correctivas si es necesario.
5. El uso de aditivos aceleradores de fraguado, endurecimiento o anticongelantes específicos para el hormigón requiere una autorización expresa de la Dirección Facultativa en cada caso, garantizando su compatibilidad y efectividad con el concreto utilizado.
B) Hormigonado en tiempo caluroso
El hormigonado en tiempo caluroso presenta desafíos que pueden afectar la calidad del concreto. Las altas temperaturas, la baja humedad relativa y la velocidad del viento pueden influir negativamente en las propiedades del hormigón, lo que podría resultar en propiedades no deseadas.
Las altas temperaturas del concreto fresco durante el tiempo caluroso aceleran el proceso de fraguado, aumentan la velocidad de hidratación y la demanda de agua, lo que puede llevar a una resistencia final más baja. Además, las condiciones de trabajo se vuelven más difíciles y aumenta el riesgo de fisuración por retracción plástica.
Por lo tanto, es importante garantizar que la temperatura del concreto al ser vertido sea inferior a 35 ºC para estructuras normales, y menos de 15 ºC para grandes masas de concreto. Durante el hormigonado en tiempo caluroso, se deben tomar medidas para evitar la evaporación del agua de la mezcla, especialmente durante el transporte del concreto, y para reducir la temperatura de la masa. Estas medidas deben intensificarse para concretos de alta resistencia.
Para prevenir los efectos adversos del tiempo caluroso en el hormigonado, es necesario proteger tanto los materiales constituyentes del hormigón como los encofrados o moldes que lo recibirán del sol directo.
Una vez que el hormigón ha sido colocado, se debe proteger del sol y especialmente del viento para evitar su deshidratación. Si la temperatura ambiente supera los 40 ºC o hay vientos excesivos, se suspenderá el hormigonado, a menos que se tomen medidas especiales con la autorización expresa de la Dirección Facultativa.
Compactación del hormigón
La compactación del hormigón es un proceso fundamental que busca aumentar su densidad, especialmente al reducir la proporción de agua-cemento. Dependiendo del tipo de consistencia requerida, se pueden emplear tres sistemas de compactación:
- Picado: Se utiliza para consistencias muy blandas o fluidas, con tongadas de espesor máximo entre 20 y 30 cm.
- Apisonado: Adecuado para consistencias blandas y plásticas, con tongadas de espesor máximo entre 15 y 20 cm.
- Vibrado: Es el sistema más común y versátil, aplicable a consistencias plásticas, blandas o secas, con tongadas de 40 a 60 cm. En este método, se vibra toda la masa de hormigón para lograr una superficie húmeda y una reducción significativa de aire.
Los vibradores pueden ser internos, externos o superficiales. En la vibración interna, se introduce una varilla vibrante en la mezcla fresca, extrayéndola de manera vertical. La vibración se detiene cuando dejan de desprenderse burbujas de aire grandes y aparece agua y/o lechada en la superficie del hormigón. En la vibración externa, se emplea un dispositivo vibrante que se coloca en uno de los lados del encofrado, generando un movimiento dentro del concreto para compactarlo.
Curado del hormigón
El curado del hormigón es crucial durante el proceso de fraguado y los primeros días de endurecimiento para garantizar su resistencia y cualidades óptimas. El tiempo de curado necesario depende del tipo y clase de cemento, así como de la temperatura y humedad ambiental.
Existen varios métodos para el curado del hormigón:
- Protección con láminas de plástico: Se cubre la superficie del hormigón con láminas de plástico para mantener la humedad y evitar la evaporación del agua.
- Protección con materiales humedecidos: Se colocan materiales como sacos de arpillera, arena, paja, entre otros, sobre la superficie del hormigón y se mantienen húmedos para retener la humedad.
- Riego con agua: Se aplica agua directamente sobre la superficie del hormigón de manera regular para mantenerlo húmedo.
- Aplicación de productos de curado: Se utilizan productos químicos especiales que forman una membrana de protección sobre la superficie del hormigón, evitando la pérdida de humedad.
Estos métodos de curado son fundamentales para asegurar que el hormigón alcance su resistencia y durabilidad óptimas.
Hormigón magro vibrado
El hormigón magro vibrado se refiere a una mezcla uniforme de áridos, cemento, agua y aditivos, utilizada en capas de base debajo de pavimentos de hormigón. Esta mezcla se coloca en obra con una consistencia que requiere el uso de vibradores internos para compactarla adecuadamente.
Hormigón de uso no estructural
Los hormigones de uso no estructural son aquellos que no contribuyen directamente a la resistencia estructural de una construcción, pero pueden mejorar las condiciones duraderas del hormigón estructural o proporcionar el volumen necesario para cumplir con ciertas geometrías requeridas para un propósito específico.
Estos hormigones se dividen en dos clases:
- Hormigón de Limpieza (HL): Su propósito es prevenir la desecación y contaminación del hormigón estructural durante su vertido y las primeras horas de fraguado. Se identifican con la clasificación HL-150/C/TM, donde la dosificación mínima de cemento es de 150 kg/m³. Se recomienda que el tamaño máximo del árido sea inferior a 30 mm para mejorar la trabajabilidad de estos hormigones.
- Hormigón No Estructural (HNE): Este tipo de hormigón se utiliza para conformar volúmenes de material resistente en elementos no críticos para la estructura. Ejemplos incluyen hormigones para aceras, bordillos y rellenos. La resistencia característica mínima de los hormigones no estructurales es de 15 N/mm².
Para facilitar la colocación de los hormigones de uso no estructural, se recomienda que el tamaño máximo del árido no supere los 40 mm. En cuanto a los materiales utilizados en su fabricación, se pueden emplear arenas y gravas rodadas, o incluso escorias siderúrgicas adecuadas.
Dado que estos hormigones suelen tener bajos contenidos de cemento, es conveniente utilizar aditivos reductores de agua para minimizar la estructura porosa del hormigón una vez endurecido. Esto contribuye a mejorar la durabilidad y las propiedades del hormigón.