Las obras de tierras comprenden aquellas que se realizan utilizando suelos naturales, ya sea procedentes de la misma obra o de préstamos cercanos. Estas obras representan las primeras etapas en la construcción de una carretera, donde se realizan movimientos de tierra como excavaciones, terraplenado y nivelación del terreno.
Sobre estas obras de tierras se ejecutan las obras de firmes. El firme se construye utilizando materiales de construcción provenientes de canteras, plantas de fabricación, entre otros recursos. Entre los materiales más comúnmente utilizados para los firmes se encuentran las zahorras artificiales, el gravacemento, las mezclas bituminosas y el hormigón. Estos materiales se utilizan para formar las capas superiores de la carretera, proporcionando una superficie resistente y duradera para el tráfico vehicular.
En resumen, las principales capas de una carretera, de abajo hacia arriba, son:
1. Terreno natural: El suelo original sobre el cual se construirá la carretera.
2. Rellenos: Capas compactadas de materiales como terraplenes, pedraplenes o todo-uno, que nivelan y estabilizan el terreno.
3. Capa subbase: Una capa intermedia que proporciona soporte adicional y mejora la capacidad de drenaje.
4. Capa base: Una capa más resistente que la subbase, que ayuda a distribuir las cargas del tráfico de manera uniforme.
5. Pavimento: La capa superior de la carretera, diseñada para soportar el tráfico vehicular y proporcionar una superficie de rodadura segura y cómoda.
Es importante tener en cuenta que cuanto más cerca esté una capa de la superficie final de la carretera, mayor calidad de materiales y de ejecución requerirá, ya que estará sujeta a mayores cargas del tráfico y desgaste.
2.1. Obras de tierra.
Las obras de tierra, también conocidas como explanaciones, comprenden todas las operaciones realizadas sobre el terreno natural para obtener una superficie resistente y con la geometría adecuada para la construcción del firme de la carretera.
Estas operaciones pueden implicar añadir capas de tierra al terreno natural, elevando así la carretera por encima de su entorno, lo que se denomina carretera en terraplén o relleno. Por otro lado, también puede ser necesario remover terreno natural, creando una especie de trinchera por donde discurrirá la carretera, lo que se conoce como carretera en desmonte.
En ocasiones, una parte de la sección transversal de la carretera se eleva en terraplén mientras que otra parte se encuentra en desmonte. En este caso, se dice que la carretera discurre a media ladera.
Sobre la superficie final de la explanación, llamada explanada, se construyen las capas del firme de la carretera. Por lo tanto, si las obras de explanación se realizan deficientemente y la carretera resultante presenta defectos, reparar estos problemas será extremadamente costoso, ya que implicará la remoción de todas las capas del firme para corregir las deficiencias en las obras de tierra.
Despeje
El despeje es una fase crucial en la construcción de la explanada de una carretera. Se refiere a la eliminación de cualquier obstáculo que pueda interferir con la obra.
Este proceso implica no solo la eliminación de árboles, sino también la demolición de estructuras como casas, almacenes u otras edificaciones que se encuentren en el área afectada por la construcción de la carretera. Las demoliciones pueden llevarse a cabo de diversas formas. Para estructuras más pequeñas, como casas de campo antiguas o corrales, una retroexcavadora suele ser suficiente. Sin embargo, en casos más complejos, pueden ser necesarias bolas de demolición de gran tamaño e incluso el uso de explosivos.
Es fundamental tener en cuenta que las demoliciones son tareas delicadas que requieren una gran precaución para garantizar la seguridad de los trabajadores y del entorno. Antes de la demolición, es necesario asegurarse de que todos los suministros de la edificación, como agua, electricidad y gas, hayan sido desconectados para evitar cualquier riesgo.
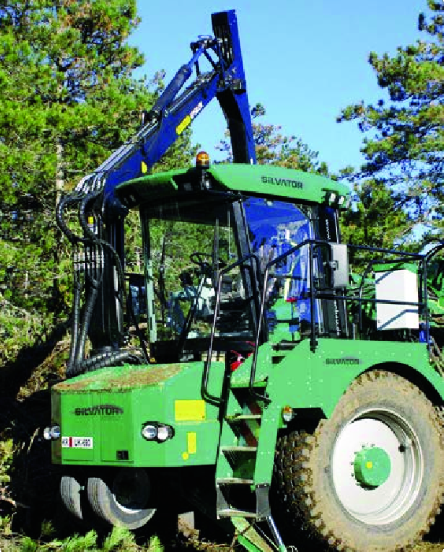
La retirada de árboles requiere consideraciones adicionales importantes. En primer lugar, los árboles que estén ubicados a menos de medio metro de la explanación también deben ser eliminados para evitar posibles daños futuros a la carretera.
Además de talar y retirar el árbol en sí, es necesario extraer su tocón, que es la parte inferior del tronco y las raíces principales. Esto asegura que no haya obstáculos subterráneos que puedan afectar la estabilidad de la carretera en el futuro.
Finalmente, el agujero dejado por la retirada del tocón debe ser rellenado para evitar hundimientos o irregularidades en el terreno. La maquinaria utilizada para la tala y retirada de árboles suele ser la misma que se emplea en tareas forestales, como motosierras y tractores. Además, existen implementos especiales para tractores que astillan las ramas de los árboles, facilitando su posterior retirada y el proceso de limpieza del terreno. Estas medidas garantizan una preparación adecuada del terreno antes de la construcción de la carretera, contribuyendo a su durabilidad y seguridad a largo plazo.
Desbroce
El desbroce se define como la eliminación de la cubierta vegetal y el suelo vegetal, extendiéndose más allá de las raíces de los arbustos. Dado que el suelo vegetal tiene un alto contenido de materia orgánica, no es adecuado para su uso en las capas de la explanación de la carretera, pero sí puede ser utilizado para plantaciones que se realizan junto a las carreteras, donde puede ser beneficioso para el crecimiento de las plantas.
La maquinaria utilizada para el desbroce es el tractor de cadenas, que cuenta con una pala potente y un escarificador trasero que abre surcos en el terreno. La acción del tractor de cadenas se complementa con el uso de una pala cargadora y camiones con volquete, que ayudan en la recolección y eliminación del material desbrozado.
Este proceso es fundamental para preparar el terreno antes de la construcción de la carretera, eliminando la vegetación y el suelo superficial para crear una superficie adecuada para la construcción de la explanación y otras capas de la carretera.
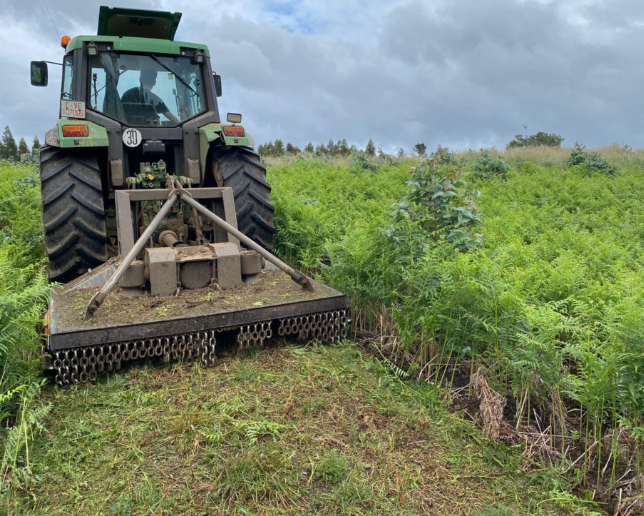
Desmontes
Los desmontes se refieren a la operación de retirar el terreno natural cuando un tramo de la carretera queda por debajo de este nivel, creando una especie de trinchera con paredes inclinadas conocidas como taludes de desmonte.
El proceso de ejecución de desmontes consta de tres fases principales:
1. Arranque del material: Esta fase implica la disgregación del terreno natural. Si el terreno es blando, se puede realizar la excavación directamente con una retroexcavadora en una operación conocida como “excavación en tierra”. En terrenos más duros, se puede utilizar el escarificador del tractor de cadenas para romper el suelo antes de la excavación con la retroexcavadora, denominada “excavación en terreno de tránsito”. En terrenos rocosos, se requerirá el uso de explosivos en una operación llamada “excavación en roca”.
2. Carga: Una vez disgregado el terreno, la carga se realiza utilizando la propia retroexcavadora o palas cargadoras, que depositan el material en el volquete de un camión o dumper.
3. Transporte y descarga: Los dumpers u otros camiones se encargan de transportar el material excavado y descargarlo en el lugar designado.
En ocasiones, cuando el terreno es blando y no tiene grandes obstáculos como rocas, se puede utilizar una máquina llamada mototraílla que puede realizar todas estas operaciones por sí misma. Las mototraíllas son costosas pero ofrecen un alto rendimiento y son rentables en grandes obras, especialmente cuando la distancia de transporte está entre 100 metros y 2 kilómetros.
Es importante aprovechar los materiales extraídos de los desmontes siempre que sea posible, utilizando aquellos que cumplan con los requisitos mínimos de calidad para los rellenos de la obra. Estos materiales no solo pueden ser reutilizados de manera eficiente, sino que también constituyen la primera fuente de suministro de materiales para la propia obra.
Dependiendo de su calidad, los materiales extraídos de los desmontes pueden ser empleados para diferentes fines, como terraplenes, todounos o pedraplenes. Por lo tanto, es fundamental planificar y ubicar adecuadamente los acopios donde se descargan estos materiales, de modo que estén disponibles para su uso en las diversas etapas de la construcción de la carretera. Esto permite optimizar los recursos y reducir los costos asociados al transporte de materiales desde otras fuentes externas.
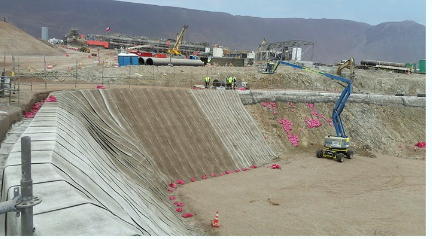
Es crucial considerar la seguridad y estabilidad de los taludes en los desmontes durante la construcción de una carretera. Los taludes, que son las paredes inclinadas creadas al retirar el terreno natural, requieren una atención especial debido a los riesgos de erosión, desprendimientos y deslizamientos que pueden presentar si no se construyen adecuadamente.
La pendiente de un talud es una característica clave que influye en su estabilidad. Cuanto menor sea la pendiente, más seguro será el talud, pero esto también conlleva un mayor volumen de terreno excavado y, por lo tanto, un costo de construcción más elevado. Factores como el tipo de terreno, la altura del talud y el flujo de agua de lluvia pueden afectar significativamente el comportamiento del talud.
En algunos casos, es necesario reforzar los taludes con anclajes para reducir el riesgo de deslizamientos superficiales. Además, es común recubrir los taludes con mallas para evitar que los desprendimientos lleguen a la calzada. También se pueden construir muros de contención de tierra, utilizando hormigón armado o gaviones (jaulas de malla rellenas de piedras), o revestir el talud con hormigón. Proteger la base del talud con muros de escollera también puede ser una medida efectiva.
Es importante planificar adecuadamente la gestión del agua de lluvia para prevenir la erosión de los taludes. Esto puede implicar la construcción de cunetas junto a las zonas más altas del talud (cunetas de guarda) y bajantes revestidas con piedras para canalizar el agua de manera segura.
Además, al pie del talud del desmonte, es fundamental construir cunetas revestidas de hormigón para dirigir el agua vertida por el talud y la propia carretera, evitando así la erosión del terreno circundante. Estas medidas son esenciales para garantizar la estabilidad y seguridad de los taludes en los desmontes a lo largo de la vida útil de la carretera.
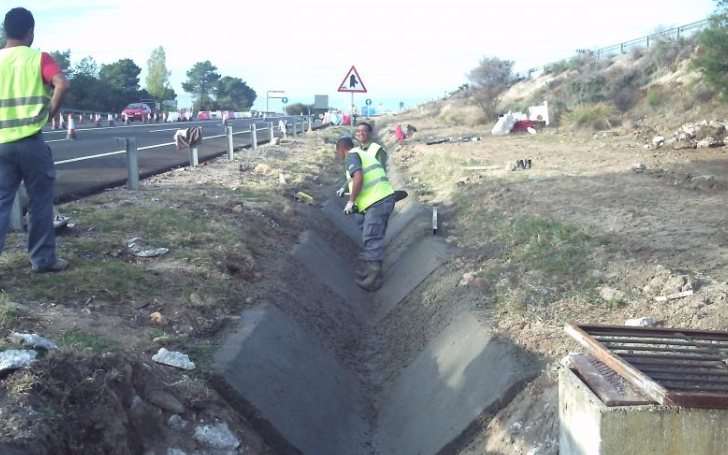
Terraplenes
Los terraplenes son estructuras construidas cuando la carretera necesita elevarse por encima del terreno natural. Estos rellenos se componen principalmente de suelos y se utilizan para elevar la carretera por encima del nivel del suelo circundante. Por otro lado, si los rellenos se construyen con rocas en lugar de suelos, se conocen como pedraplenes.
Un terraplén típico está compuesto por varias zonas distintas, cada una con una función específica. Estas zonas pueden incluir:
- La base, que es la capa inferior del terraplén y proporciona una base sólida y estable para el relleno.
- La zona de transición, que es la parte intermedia del terraplén y ayuda a distribuir uniformemente las cargas.
- La capa superior, que es la parte superior del terraplén y proporciona una superficie nivelada para la carretera.
Estas zonas se construyen cuidadosamente para garantizar la estabilidad y durabilidad del terraplén, así como para proporcionar una base sólida para la carretera que se construirá sobre él.
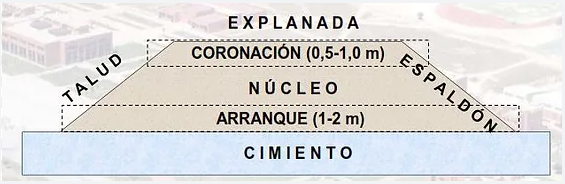
La construcción de un terraplén implica una serie de consideraciones importantes en cuanto a la inclinación y la estructura del relleno. Por ejemplo, la capa de coronación, que es la parte superior del terraplén, no es horizontal en sentido transversal, sino que tiene una pendiente. Esta pendiente puede ser única o doble, con dos planos inclinados opuestos unidos por el eje de la carretera, lo que se conoce como bombeo. Esta falta de horizontalidad se debe a la futura rasante de la carretera, ya que la explanada y la rasante siempre son paralelas. Estas pendientes son necesarias para favorecer el drenaje del agua fuera de la carretera y proporcionar peralte en las curvas.
Las características de cada zona del relleno son las siguientes:
- Cimiento del relleno: Es el terreno natural existente debajo del relleno. Si este terreno es poco compacto, se debe escarificar, regar y compactar. Si el terreno natural no tiene la calidad adecuada, se puede retirar y reemplazar con otro suelo de mejor calidad para formar la primera capa del relleno. Su espesor mínimo suele ser de 1 metro.
- Arranque: Constituye las primeras capas del relleno y puede considerarse parte del núcleo del terraplén.
- Núcleo: Es el conjunto de capas situadas entre el cimiento y la coronación, formando el cuerpo principal del relleno.
- Espaldón: Es el material que cubre lateralmente al núcleo y lo protege de las condiciones climáticas. Constituye la parte exterior del terraplén y, en algunas ocasiones, puede formar o estar integrado en los taludes del relleno.
- Coronación: Son las últimas dos o tres capas del relleno, formando la parte superior del terraplén. La superficie final de la coronación se denomina explanada y es donde se construirá la carretera.
Es importante tener en cuenta que a medida que ascendemos en las capas del terraplén, la calidad de los materiales y el nivel de compactación aumentan. Por ejemplo, las capas de la coronación, que son las capas superiores del terraplén y estarán más expuestas a las cargas del tráfico y a las condiciones climáticas, estarán compuestas por suelos seleccionados o incluso estabilizados. Estos suelos se someten a una compactación vigorosa para asegurar su estabilidad y durabilidad a largo plazo.
Por otro lado, las primeras capas del terraplén, que están más alejadas de la superficie y por lo tanto sufren menos las cargas del tráfico, pueden estar constituidas por suelos de calidad media-baja y menos compactados. Esto se debe a que estas capas no están tan expuestas a las tensiones y esfuerzos como las capas superiores, por lo que se requiere un nivel de calidad y compactación menor.
Esta diferenciación en la calidad de los materiales y el nivel de compactación en las diferentes capas del terraplén es fundamental para garantizar la estabilidad y la durabilidad de la estructura del terraplén en su conjunto, así como para proporcionar una base sólida y segura para la construcción de la carretera.
Aquí tienes un resumen de las especificaciones que deben cumplir los distintos tipos de suelos para terraplenes:
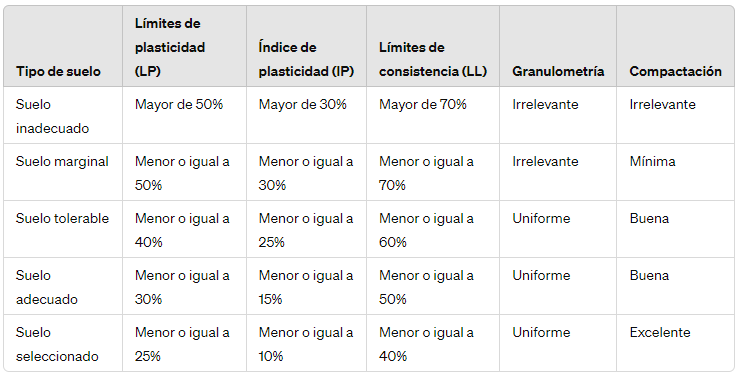
Estas especificaciones se refieren a los límites de plasticidad, los límites de consistencia, la granulometría y el nivel de compactación requeridos para cada tipo de suelo. Es importante realizar estos ensayos de identificación en laboratorio para clasificar adecuadamente los suelos y garantizar que se utilicen los materiales adecuados en la construcción de los terraplenes.
La construcción de terraplenes es una etapa crítica en la obra de una carretera, ya que cualquier defecto en esta parte puede causar problemas como hundimientos, baches e incluso socavones, a pesar de que las capas superiores del firme estén bien ejecutadas.
Los lugares de donde se obtienen los suelos para construir terraplenes se llaman préstamos. En estos sitios se carga el suelo y se transporta a la zona de construcción utilizando camiones o traíllas.
Las fases de la construcción de terraplenes son las siguientes:
1. Extensión: Los terraplenes se construyen mediante la colocación de capas sucesivas que, una vez compactadas, no deben superar un espesor de 30 cm para asegurar una compactación adecuada en toda la capa. En suelos de baja calidad y difícil compactación, como suelos arcillosos, el espesor de las capas debe ser aún menor. La motoniveladora es la maquinaria principal utilizada para extender el suelo, aunque la mototraílla también puede realizar esta tarea.
Durante la ejecución de los trabajos, la superficie de cada capa debe tener la pendiente transversal necesaria, generalmente alrededor del cuatro por ciento (4%), para garantizar el drenaje adecuado del agua y prevenir la erosión. En rellenos de más de 5 m de altura, o en casos donde se espera una erosión significativa, se construyen caballones de tierra en los bordes de las capas para dirigir el flujo de agua hacia bajantes diseñadas para controlar las aguas de escorrentía.
Es crucial asegurarse de que todo el perfil del terraplén quede correctamente compactado. Para lograr esto, a veces se proporciona un ancho adicional a la capa para permitir que el compactador se acerque al borde, y luego se recorta el talud para darle la forma deseada.
La etapa de compactación es crucial para garantizar la calidad del terraplén. Para lograr una compactación adecuada, es necesario seleccionar el tipo correcto de compactador, controlar la humedad del suelo, ajustar el espesor de cada capa y determinar el número de pasadas necesarias. Se suelen realizar tramos de prueba fuera del área de trabajo principal para evaluar estas variables. El punto de referencia para la compactación es la densidad Próctor obtenida en el ensayo de laboratorio.
Al medir la densidad alcanzada en el sitio de la obra después de la compactación, se compara con la densidad Próctor para determinar si se ha logrado una compactación satisfactoria. En la coronación de un terraplén, se espera que el porcentaje de densidad en obra sea mayor al 100%, mientras que en el resto de las capas debe ser superior al 95%.
Por ejemplo, si la densidad Próctor obtenida en laboratorio es de 2.12 g/cm3 y la densidad medida en el sitio de la obra después de la compactación de la coronación es de 2.09 g/cm3, el cálculo del porcentaje de compactación sería: (2.09 / 2.12) x 100 = 98.6%. En este caso, la compactación sería insuficiente ya que no alcanza el 100%.
En la práctica, no se compara directamente la medición de densidad en obra con la densidad Próctor de laboratorio. En su lugar, el suelo se divide en lotes de control que se aceptan o rechazan en su totalidad.
Entonces, el concepto de lote se define como una sección de la carretera con ciertas dimensiones específicas donde se llevan a cabo mediciones de densidad para evaluar la calidad de la compactación del terraplén. La selección y evaluación de los lotes se rigen por criterios como la longitud de la carretera, la superficie de la coronación del terraplén y la altura del terraplén.
Para cada lote, se realizan cinco mediciones de densidad y se calcula el promedio. Si este promedio supera el mínimo establecido, se considera que el lote cumple con los estándares de compactación. Incluso si algunas de las mediciones individuales están ligeramente por debajo del valor mínimo, siempre que las demás compensen este déficit, el lote puede ser aceptado. Además, las humedades de los puntos medidos deben estar cerca de la humedad óptima Próctor, permitiéndose variaciones dentro de un rango específico.
El método de compactación y la densidad objetivo varían según el tipo de suelo y las especificaciones del proyecto. El ensayo Próctor Normal y el Próctor Modificado son métodos comunes para determinar la densidad máxima de un suelo bajo diferentes condiciones de compactación. El Próctor Modificado suele resultar en una densidad mayor que el Próctor Normal para un mismo suelo, lo que implica un mayor esfuerzo de compactación para alcanzar densidades próximas o superiores a la densidad máxima Próctor Modificado.
En la actualidad, las mediciones de densidad en obra se realizan principalmente con nucleodensímetros, que son dispositivos que emplean radiación para medir la densidad del suelo. Estos dispositivos pueden realizar múltiples mediciones en una hora y también proporcionan información sobre la humedad del suelo. Los operadores de nucleodensímetros deben estar especializados y titulados para manejar este equipo de forma segura y precisa. Durante la medición, la sonda del nucleodensímetro se introduce en el suelo previamente compactado hasta una profundidad de aproximadamente 30 cm, y se toman lecturas en diferentes puntos para evaluar la uniformidad de la compactación.
La selección del equipo de compactación adecuado depende del tipo de suelo. Los suelos granulares o poco arcillosos, como gravas y arenas, se compactan mejor con un compactador de rodillo liso vibrante. Por otro lado, los suelos claramente arcillosos se compactan de manera más efectiva con un rodillo de pata de cabra.
La humedad del suelo es un factor crucial para la compactación exitosa. El ensayo Proctor ayuda a determinar la humedad óptima para la compactación. Durante la compactación en obra, la humedad del suelo debe ser similar a la humedad óptima determinada por el ensayo Proctor. En la mayoría de los casos, es necesario añadir agua al suelo para alcanzar la humedad óptima. Es preferible realizar este proceso de humectación en el acopio antes de extender el suelo. Sin embargo, si la capa extendida aún carece de humedad suficiente, se puede aplicar un riego adicional con un camión cisterna.
En situaciones donde el suelo tiene un exceso de humedad debido a lluvias recientes, se debe permitir que la capa se airee para que parte del exceso de humedad se evapore. Sin embargo, si el suelo es naturalmente muy húmedo, como en el caso de las arcillas, dejar que se airee puede no ser efectivo. En estos casos, puede ser necesario estabilizar el suelo con cal para mejorar su comportamiento durante la compactación.
En resumen, es preferible que el suelo tenga una humedad ligeramente inferior a la óptima durante la compactación, en lugar de tener una humedad excesiva.
El exceso de compactación puede tener consecuencias negativas, como la ruptura de una capa de suelo. En estos casos, es necesario escarificar la capa dañada y volver a ejecutarla. Esta situación suele ocurrir cuando las medidas de densidad no cumplen con los requisitos del proyecto y, como solución, se intenta compactar el suelo repetidamente sin considerar que la humedad del suelo no es óptima para una compactación efectiva.
Para verificar la calidad de la compactación, se realiza un ensayo obligatorio llamado ensayo de carga del suelo con placa. En este ensayo, se carga el suelo con una placa que transmite presión y se mide el descenso de la placa a medida que se aumenta la presión. La presión se aplica mediante un gato hidráulico, y como elemento de reacción se utiliza comúnmente un camión cargado. Este ensayo proporciona información importante sobre la capacidad del suelo para soportar cargas y su resistencia a la compresión.
Pedraplenes
Los pedraplenes son rellenos construidos con fragmentos de rocas de gran tamaño, generalmente extraídas de los desmontes de la propia carretera. En comparación con los terraplenes, presentan varias ventajas significativas:
1. Mayor rapidez de construcción: Debido a que el espesor de las capas de pedraplenes es mayor, se pueden construir más rápidamente en comparación con los terraplenes.
2. Taludes más verticales: Los pedraplenes permiten taludes más verticales, lo que significa que ocupan menos superficie y volumen en comparación con los terraplenes.
3. Mayor resistencia a la inundación y erosión superficial: Los pedraplenes son más capaces de soportar la inundación por agua durante períodos prolongados, así como la erosión superficial causada por la lluvia.
El uso de pedraplenes en lugar de terraplenes está recomendado en situaciones como:
- Rellenos de gran altura.
- Parte inferior de rellenos sujetos a inundación o encharcamiento. Sin embargo, no todas las rocas extraídas de los desmontes son adecuadas para construir pedraplenes. Las rocas deben ser resistentes e inalterables a la acción del agua, lo cual se puede evaluar mediante ensayos de laboratorio.
Además, la forma de las rocas es un factor importante. Se debe limitar el contenido de fragmentos con forma plana o alargada, ya que pueden romperse durante la compactación o durante la vida útil de la carretera debido al tráfico. Los fragmentos con forma inadecuada no deben representar más del 30% del peso total de todos los fragmentos, y las formas cúbicas o esféricas son las más adecuadas.
Las condiciones granulométricas para el material destinado a pedraplenes son fundamentales para garantizar su adecuado desempeño y resistencia. Estas condiciones incluyen:
1. Contenido de partículas pequeñas: El contenido de partículas de tamaño inferior a 20 mm debe ser inferior al 30% en peso. Esto asegura que el material esté compuesto principalmente por fragmentos grandes, que proporcionan estabilidad al pedraplén.
2. Contenido de partículas muy finas: El contenido de partículas de tamaño inferior a 0,080 mm debe ser inferior al 10% en peso. Las partículas muy finas pueden comprometer la capacidad de drenaje del pedraplén y afectar su estabilidad.
3. Tamaño máximo y mínimo: El tamaño máximo de las partículas debe ser de al menos 100 mm y como máximo 900 mm. Esto garantiza que las rocas sean lo suficientemente grandes para proporcionar resistencia al pedraplén, pero no tan grandes como para dificultar la compactación.
Es importante tener en cuenta que estas condiciones se aplican al material una vez compactado. Se recomienda que la curva granulométrica total del material compactado se encuentre dentro de un rango específico para garantizar su idoneidad y estabilidad en el pedraplén.
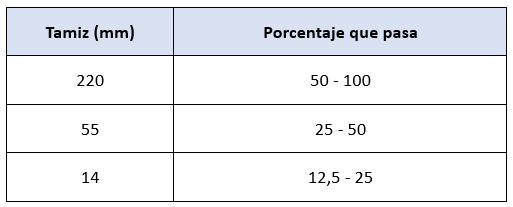
El pedraplén, al igual que cualquier otro tipo de relleno, se compone de varias partes fundamentales que cumplen funciones específicas. Aquí están las descripciones de cada parte:
- Cimiento: Es la parte inferior del pedraplén que está en contacto con el terreno preexistente o la superficie de apoyo. Su función principal es proporcionar estabilidad y distribuir las cargas del relleno de manera uniforme sobre el terreno subyacente. El espesor mínimo del cimiento es de un metro o la altura máxima libre desde la superficie de apoyo hasta la zona de transición del pedraplén, si esta altura es inferior a un metro.
- Núcleo: Es la parte central del pedraplén que se encuentra entre el cimiento y la zona de transición. Contribuye a la estabilidad estructural del relleno y ayuda a distribuir las cargas de manera eficiente.
- Espaldones: Son las partes exteriores del relleno que sirven como refuerzo y protección lateral. A menudo forman parte de los taludes del pedraplén y proporcionan estabilidad adicional al relleno.
- Transición: Esta zona se encuentra en la parte superior del pedraplén y actúa como una capa de transición entre el relleno de pedraplén y el terraplén. Tiene un espesor mínimo de un metro y consta de dos tongadas. La transición es una característica única de los pedraplenes y no se encuentra en los terraplenes.
- Coronación: Es la capa final del pedraplén, que se compone de material de terraplén y proporciona una superficie sólida y plana para apoyar las capas del firme de la carretera.
– La construcción de un pedraplén implica varias etapas, que incluyen la preparación de la superficie de apoyo, la colocación y compactación del material del pedraplén, y la creación de la transición y la coronación. Cada fase es crucial para garantizar la estabilidad y durabilidad del relleno de pedraplén.
– Excavación y transporte de rocas: En esta fase, se utilizan martillos hidráulicos y retroexcavadoras para romper el suelo rocoso en las áreas designadas para el desmonte. Si es necesario, también se pueden emplear explosivos. Una vez que las rocas están sueltas, se utilizan palas cargadoras y camiones volquete para transportar el material rocoso a la zona donde se construirá el pedraplén. Es crucial que la zona de desmonte esté lo más cerca posible de la ubicación del relleno para minimizar los costos y la distancia de transporte.
– Extendido y compactación: Similar al proceso de construcción de terraplenes, el pedraplén se construye por capas o tongadas. Sin embargo, las capas de un pedraplén tienen un espesor mucho mayor que las de un terraplén, generalmente entre 60 y 135 cm. Las capas de rocas se extienden utilizando maquinaria como tractores de cadenas o equipos similares. Luego, se compactan utilizando compactadores adecuados para el tipo de roca utilizado. Dependiendo de la naturaleza de las rocas, la compactación puede realizarse en húmedo o en seco. Si las rocas tienen cierta capacidad de absorción de agua o si hay fragmentos finos o arena presentes, la adición de agua puede ayudar en el proceso de compactación.
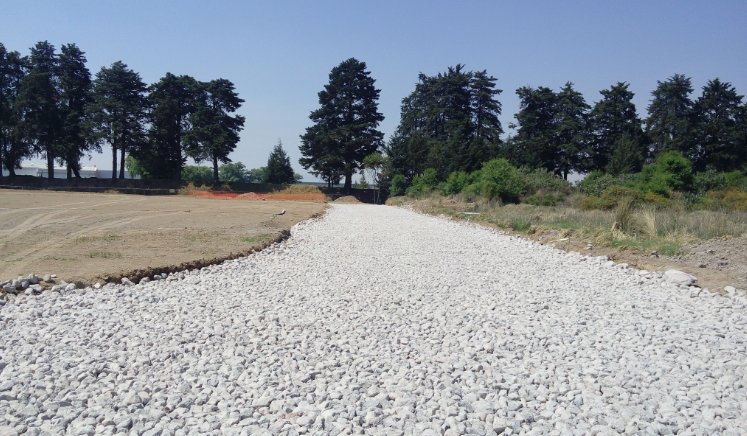
Todouno
El material todouno es aquel que se encuentra entre los suelos para terraplenes y las rocas para pedraplenes en términos de tamaño de partículas. Según lo indicado en el artículo 333 del PG-3, su granulometría debe cumplir ciertas condiciones:
- El contenido de partículas inferiores a 0,080 mm debe ser inferior al 35 % y el contenido de partículas inferiores a 20 mm debe ser igual o superior al 30 % y igual o inferior al 70 %.
- O bien, el contenido de partículas inferiores a 20 mm debe ser inferior al 30 %, pero deben tener un contenido en finos (material inferior a 0,080 mm) igual o superior al 10 %.
- Además, también se consideran materiales para rellenos todouno aquellos que cumplen las condiciones granulométricas de pedraplén, pero en los que el tamaño máximo es inferior a 100 mm.
Estas condiciones se aplican al material compactado. El material todouno generalmente proviene de las excavaciones de la propia obra.
Las partes de un relleno todouno son similares a las del pedraplén, incluyendo cimiento, núcleo, espaldones, transición y coronación. Sin embargo, el espesor de las tongadas en un relleno todouno es menor, oscilando entre 40 y 60 cm, y siempre debe ser superior a 1,5 veces el tamaño máximo del material.
Explanadas
Las explanadas son la superficie final de las obras de tierras sobre la cual se apoyarán las capas del firme de la carretera. Para que una explanada sea adecuada, debe cumplir con varios requisitos:
1. Ser paralela a la rasante de la carretera: Debe seguir la misma inclinación que la carretera para garantizar un buen drenaje.
2. Ser poco sensible a las variaciones de humedad: Debe tener una composición que minimice los cambios dimensionales causados por variaciones en la humedad.
3. Tener pendientes adecuadas para evacuar las aguas de lluvia: Debe contar con pendientes que permitan un drenaje efectivo de las aguas pluviales durante la obra.
4. Resistir el tráfico de la maquinaria de obra sin deformarse: Debe ser lo suficientemente resistente para soportar la carga de la maquinaria utilizada durante la construcción sin sufrir deformaciones excesivas.
5. Tener una geometría libre de irregularidades: Debe presentar una superficie uniforme y libre de desniveles que puedan afectar negativamente a la construcción de las capas del firme.
La norma española 6.1-IC “Secciones de firme” define tres categorías de explanadas: E1, E2 y E3. El tipo de explanada obtenido se determina mediante un ensayo de carga con placa y el cálculo del módulo de compresibilidad a partir de este ensayo. Sin embargo, la norma proporciona ejemplos de rellenos que equivalen a cada categoría de explanada, lo que permite al proyectista seleccionar la opción más adecuada para el proyecto. Una vez construida, la explanada debe ser ensayada mediante una placa de carga para verificar su categoría.
La elección del tipo de explanada depende de varios factores, como los materiales disponibles y la intensidad del tráfico pesado que se espera en la carretera. Además, el tipo de explanada seleccionado influirá en las capas del firme que se construirán sobre ella.
Estabilización de suelos
La estabilización de suelos es un proceso que busca mejorar notablemente las propiedades del suelo mediante la adición de aditivos, siendo la cal y el cemento los más comunes. Otros aditivos utilizados incluyen escorias, ligantes hidrocarbonatos, cloruro de sodio y cloruro de calcio. El objetivo principal de la estabilización es aumentar la resistencia del suelo y reducir su susceptibilidad al agua.
Al estabilizar un suelo, se pueden emplear materiales de baja o media calidad para rematar las explanaciones, lo que permite aprovechar materiales de la propia obra que, de otro modo, solo serían adecuados para las capas más profundas de los rellenos.
La efectividad de la estabilización depende de varios factores, incluyendo el tipo de suelo, el tipo y la cantidad de aditivo estabilizador utilizado, y la ejecución en obra.
La cal es uno de los materiales de construcción más utilizados para estabilizar suelos, especialmente en suelos arcillosos con alta humedad natural. La dosificación de cal suele oscilar entre el 2 y el 7% en relación con el suelo.
Los efectos beneficiosos de la adición de cal a un suelo incluyen la reducción del índice de plasticidad (IP), el aumento de la humedad óptima de compactación, lo que permite una compactación más densa de los suelos plásticos con alta humedad natural, y el aumento de la resistencia del suelo.
El cemento es el aditivo más utilizado para mejorar y estabilizar suelos. Cuando necesitamos mejorar las propiedades de un suelo de calidad media-baja que contiene arcillas, hablamos de suelo mejorado con cemento en lugar de suelo estabilizado. Con pequeñas cantidades de cemento (generalmente no más del 3 o 4%), se mejora considerablemente la resistencia del suelo. De esta manera, obtenemos suelos mejorados conocidos como S-EST 1 (contienen al menos un 2% de cemento) y S-EST 2 (de mayor resistencia, ya que contienen al menos un 3% de cemento).
Por otro lado, cuando en la obra disponemos o traemos de un préstamo un suelo granular de buena calidad (suelos sueltos que contienen gravas y arenas, pero pocas arcillas), hablamos de suelo estabilizado con cemento, ya que la adición de cemento lo transforma en un material rígido y resistente, similar a un hormigón pobre. Los porcentajes de cemento agregados en este caso suelen oscilar entre el 3% y el 8%. La explanada que se obtiene con este tipo de suelo es de tipo E3, es decir, la más resistente. Al suelo estabilizado con cemento se le denomina S-EST 3.
Para lograr suelos mejorados o estabilizados, se requieren ensayos previos en laboratorio que determinen el contenido óptimo de cemento y agua que se añadirá al suelo.
La estabilización de suelos con cal o cemento consta de varias fases:
1. Disgregación del suelo: En esta etapa, se rompen los terrones y se desintegran las partículas del suelo para facilitar la mezcla homogénea con los aditivos.
2. Humectación (o desecación, si fuera necesario) del suelo: Se ajusta el contenido de humedad del suelo para alcanzar la humedad óptima de compactación. En algunos casos, es necesario secar el suelo si su contenido de humedad es excesivo.
3. Dosificación del cemento o la cal: Se determina la cantidad adecuada de cemento o cal que se debe agregar al suelo para lograr las propiedades deseadas de estabilización. Esta dosificación se basa en ensayos previos en laboratorio y consideraciones específicas del proyecto.
4. Mezclado: Se mezcla el suelo con el cemento o la cal de manera homogénea para asegurar una distribución uniforme de los aditivos. Esta mezcla puede realizarse mecánicamente utilizando estabilizadores especializados o maquinaria agrícola como tractores con gradas de discos o rotavatores.
5. Compactación: Una vez que el suelo ha sido mezclado con los aditivos, se procede a compactarlo utilizando compactadores para alcanzar la densidad requerida. La compactación es crucial para mejorar la resistencia y estabilidad del suelo estabilizado.
6. Ejecución de juntas: Se realizan juntas para controlar y prevenir la aparición de grietas y fisuras en la superficie del suelo estabilizado. Estas juntas pueden ser cortes o ranuras que se realizan durante el proceso de compactación.
7. Curado: Después de la compactación, se lleva a cabo un proceso de curado para permitir que los aditivos reaccionen con el suelo y se desarrollen las propiedades de estabilización. Este proceso puede implicar la aplicación de agua u otros métodos de curado para garantizar un resultado óptimo.
La máquina estabilizadora es una herramienta fundamental en el proceso de estabilización de suelos. Está equipada con un rotor-fresador que se encarga de disgregar el suelo para facilitar su mezcla con los aditivos. Además, cuenta con un depósito para agregar agua y realizar la dosificación de cemento o cal de manera controlada.
Es importante que la dosificación de cemento o cal se realice en forma de lechada, es decir, en estado líquido, para asegurar una distribución uniforme de los aditivos en toda la mezcla. El mezclado debe ser completo, abarcando toda la anchura y profundidad de la capa que se está estabilizando, lo cual suele ser garantizado por las máquinas estabilizadoras. Una señal de un buen mezclado es la uniformidad del color del suelo, indicando una distribución homogénea de los aditivos, y la ausencia de grumos, que denotarían una mezcla heterogénea.
Dado que el cemento y la cal fraguan al entrar en contacto con el agua, es crucial que la compactación del suelo estabilizado comience inmediatamente después del mezclado y finalice antes de que comience el fraguado de la mezcla. De lo contrario, la compactación podría causar fracturas en el suelo estabilizado. Por esta razón, el material estabilizado con cemento no debe permanecer más de media hora sin iniciar la compactación, según lo estipulado por el artículo 512 del PG-3.
El control de la compactación y las sucesivas pasadas de compactación, si fueran necesarias, se realizan con premura utilizando equipos de medición de densidad en obra. Esto se hace rápidamente para evitar que el fraguado comience antes de que se complete el proceso de compactación.
Después de extender y compactar una franja de suelo estabilizado, se procede a realizar la siguiente franja mientras el borde de la primera franja esté en condiciones adecuadas para la compactación. Si esto no fuera posible, se ejecutará una junta longitudinal, aunque se debe evitar en la medida de lo posible. Entre las pasadas sucesivas del estabilizador, se debe asegurar un solape transversal para evitar zonas insuficientemente tratadas o la acumulación de segregaciones. Por lo general, este solape oscila entre quince y veinticinco centímetros.
En el caso de estabilizaciones con cemento, se deben disponer juntas transversales de trabajo en las áreas donde se interrumpa el proceso constructivo por un tiempo superior al período de trabajabilidad de la mezcla. Estas juntas transversales de trabajo se realizan disgregando el material de una zona ya tratada en una longitud suficiente, generalmente no menos de un diámetro del rotor-fresador, y bajando hasta la profundidad especificada sin avanzar, para permitir la incorporación precisa de la cal o el cemento en la zona no tratada.
Una vez finalizada la compactación, se deja que la capa endurezca. Cuando la resistencia de la capa lo permita, se riega con agua para mantener húmeda la superficie. Posteriormente, se realiza un riego con emulsión bituminosa para evitar una pérdida rápida de humedad de la capa. Este proceso se conoce como curado y contribuye a mejorar la durabilidad y resistencia de la capa estabilizada.
Cuando la capa de suelo estabilizado no constituya la coronación de la explanada, es decir, cuando no sea la última capa de las obras de tierras, se puede prescindir del riego de curado si se mantiene la superficie húmeda durante un período mínimo de tres a siete días a partir de su terminación.
En el caso de suelos estabilizados con cemento que formen capas de coronación para la formación de explanadas de categoría E1, E2 y E3, mientras la compactación, la terminación de la superficie y el curado final del suelo estabilizado con cemento estén en proceso, se prohíbe toda circulación que no sea imprescindible para estas operaciones. Después de ejecutar el riego de curado, no se permitirá la circulación de vehículos ligeros durante los tres primeros días ni de vehículos pesados durante los siete primeros días. Por lo tanto, la siguiente capa de la obra no podrá comenzar a ejecutarse antes de una semana.
En el caso de estabilizaciones con cal y si se utilizaron rodillos cuyo peso individual fuera superior a veinticinco toneladas (25 t) para la compactación, el director de las obras puede autorizar la puesta en obra de la siguiente capa de firme inmediatamente después de la terminación de la superficie, prescindiendo del curado final.